3D scanner
From Wikipedia, the free encyclopedia
![]() |
|
Basics | |
---|---|
3D modeling / 3D scanning | |
3D rendering / 3D printing | |
3D computer graphics software | |
Primary Uses | |
3D models / Computer-aided design | |
Graphic design / Video games | |
Visual effects / Visualization | |
Virtual engineering / Virtual reality | |
Related concepts | |
CGI / Animation / 3D display | |
Wireframe model / Texture mapping | |
Computer animation / Motion capture | |
Skeletal animation / Crowd simulation | |
Global illumination / Volume rendering | |
A 3D scanner is a device that analyzes a real-world object or environment to collect data on its shape and possibly its appearance (i.e. color). The collected data can then be used to construct digital, three dimensional models useful for a wide variety of applications. These devices are used extensively by the entertainment industry in the production of movies and video games. Other common applications of this technology include industrial design, orthotics and prosthetics, reverse engineering and prototyping, quality control/inspection and documentation of cultural artifacts.
Many different technologies can be used to build these 3D scanning devices; each technology comes with its own limitations, advantages and costs. It should be remembered that many limitations in the kind of objects that can be digitized are still present: for example optical technologies encounter many difficulties with shiny, mirroring or transparent objects.
There are however methods for scanning shiny objects, such as covering them with a thin layer of white powder that will help more light photons to reflect back to the scanner. Laser scanners can send trillions of light photons toward an object and only receive a small percentage of those photons back via the optics that they use. The reflectivity of an object is based upon the object's color or terrestrial albedo. A white surface will reflect lots of light and a black surface will reflect only a small amount of light. Transparent objects such as glass will only refract the light and give false three dimensional information.
Contents
|
[edit] Functionality
The purpose of a 3D scanner is usually to create a point cloud of geometric samples on the surface of the subject. These points can then be used to extrapolate the shape of the subject (a process called reconstruction). If color information is collected at each point, then the colors on the surface of the subject can also be determined.
3D scanners are very analogous to cameras. Like cameras, they have a cone-like field of view, and like cameras, they can only collect information about surfaces that are not obscured. While a camera collects color information about surfaces within its field of view, 3D scanners collect distance information about surfaces within its field of view. The “picture” produced by a 3D scanner describes the distance to a surface at each point in the picture. If a spherical coordinate system is defined in which the scanner is the origin and the vector out from the front of the scanner is φ=0 and θ=0, then each point in the picture is associated with a φ and θ. Together with distance, which corresponds to the r component, these spherical coordinates fully describe the three dimensional position of each point in the picture, in a local coordinate system relative to the scanner.
For most situations, a single scan will not produce a complete model of the subject. Multiple scans, even hundreds, from many different directions are usually required to obtain information about all sides of the subject. These scans have to be brought in a common reference system, a process that is usually called alignment or registration, and then merged to create a complete model. This whole process, going from the single range map to the whole model, is usually known as the 3D scanning pipeline.[1]
[edit] Technology
The two types of 3D scanners are contact and non-contact. Non-contact 3D scanners can be further divided into two main categories, active scanners and passive scanners. There are a variety of technologies that fall under each of these categories.
[edit] Contact
Contact 3D scanners probe the subject through physical touch. A CMM (coordinate measuring machine) is an example of a contact 3D scanner. It is used mostly in manufacturing and can be very precise. The disadvantage of CMMs though, is that it requires contact with the object being scanned. Thus, the act of scanning the object might modify or damage it. This fact is very significant when scanning delicate or valuable objects such as historical artifacts. The other disadvantage of CMMs is that they are relatively slow compared to the other scanning methods. Physically moving the arm that the probe is mounted on can be very slow and the fastest CMMs can only operate on a few hundred hertz. In contrast, an optical system like a laser scanner can operate from 10 to 500 kHz.
Other examples are the hand driven touch probes used to digitize clay models in computer animation industry.
[edit] Non-contact active
Active scanners emit some kind of radiation or light and detect its reflection in order to probe an object or environment. Possible types of emissions used include light, ultrasound or x-ray.
[edit] Time-of-flight
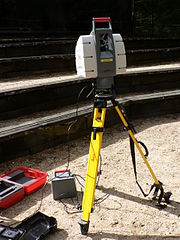
The time-of-flight 3D laser scanner is an active scanner that uses laser light to probe the subject. At the heart of this type of scanner is a time-of-flight laser rangefinder. The laser rangefinder finds the distance of a surface by timing the round-trip time of a pulse of light. A laser is used to emit a pulse of light and the amount of time before the reflected light is seen by a detector is timed. Since the speed of light c is a known, the round-trip time determines the travel distance of the light, which is twice the distance between the scanner and the surface. If t is the round-trip time, then distance is equal to . The accuracy of a time-of-flight 3D laser scanner depends on how precisely we can measure the t time: 3.3 picoseconds (approx.) is the time taken for light to travel 1 millimetre.
The laser rangefinder only detects the distance of one point in its direction of view. Thus, the scanner scans its entire field of view one point at a time by changing the range finder’s direction of view to scan different points. The view direction of the laser rangefinder can be changed by either rotating the range finder itself, or by using a system of rotating mirrors. The latter method is commonly used because mirrors are much lighter and can thus be rotated much faster and with greater accuracy. Typical time-of-flight 3D laser scanners can measure the distance of 10,000~100,000 points every second.
[edit] Triangulation
The triangulation 3D laser scanner is also an active scanner that uses laser light to probe the environment. With respect to time-of-flight 3D laser scanner the triangulation laser shines a laser on the subject and exploits a camera to look for the location of the laser dot. Depending on how far away the laser strikes a surface, the laser dot appears at different places in the camera’s field of view. This technique is called triangulation because the laser dot, the camera and the laser emitter form a triangle. The length of one side of the triangle, the distance between the camera and the laser emitter is known. The angle of the laser emitter corner is also known. The angle of the camera corner can be determined by looking at the location of the laser dot in the camera’s field of view. These three pieces of information fully determine the shape and size of the triangle and gives the location of the laser dot corner of the triangle. In most cases a laser stripe, instead of a single laser dot, is swept across the object to speed up the acquisition process. The National Research Council of Canada was among the first institutes to develop the triangulation based laser scanning technology in 1978.[2]
[edit] Notes on time-of-flight and triangulation scanners
Time-of-flight and triangulation range finders each have strengths and weaknesses that make them suitable for different situations. The advantage of time-of-flight range finders is that they are capable of operating over very long distances, on the order of kilometers. These scanners are thus suitable for scanning large structures like buildings or geographic features. The disadvantage of time-of-flight range finders is their accuracy. Due to the high speed of light, timing the round-trip time is difficult and the accuracy of the distance measurement is relatively low, on the order of millimeters. Triangulation range finders are exactly the opposite. They have a limited range of some meters, but their accuracy is relatively high. The accuracy of triangulation range finders is on the order of tens of micrometers.
Time of flight scanners accuracy can be lost when the laser hits the edge of an object because the information that is sent back to the scanner is from two different locations for one laser pulse. The co-ordinate relative to the scanners position for a point that has hit the edge of an object will be calculated based on an average and therefore will put the point in the wrong place. When using a high resolution scan on an object the chances of the beam hitting an edge are increased and the resulting data will show noise just behind the edges of the object. Scanners with a smaller beam width will help to solve this problem but will be limited by range as the beam width will increase over distance. Software can also help by determining that the first object to be hit by the laser beam should cancel out the second.
At a rate of 10,000 sample points per second, low resolution scans can take less than a second, but high resolution scans, requiring millions of samples, can take minutes for some time-of-flight scanners. The problem this creates is distortion from motion. Since each point is sampled at a different time, any motion in the subject or the scanner will distort the collected data. Thus, it is usually necessary to mount both the subject and the scanner on stable platforms and minimize vibration. Using these scanners to scan objects in motion is very difficult.
Recently, there has been research on compensating for distortion from small amounts of vibration.[3]
When scanning in one position for any length of time slight movement can occur in the scanner position due to changes in temperature. If the scanner is set on a tripod and there is strong sunlight on one side of the scanner then that side of the tripod will expand and slowly distort the scan data from one side to another. Some laser scanners have level compensator built into them to counteract any movement of the scanner during the scan process.
[edit] Conoscopic holography
In a Conoscopic system a laser beam is projected onto the surface and then the immediate reflection along the same ray-path are put through a conoscopic crystal and projected onto a CCD. The result is a diffraction pattern, that can be frequency analyzed to determine the distance to the measured surface. The main advantage with Conoscopic Holography is that only a single ray-path is needed for measuring, thus giving an opportunity to measure for instance the depth of a finely drilled hole.
[edit] Handheld laser
Handheld laser scanners create a 3D image through the triangulation mechanism described above: a laser dot or line is projected onto an object from a handheld device and a sensor (typically a charge-coupled device or position sensitive device) measures the distance to the surface.
Data is collected in relation to an internal coordinate system and therefore to collect data where the scanner is in motion the position of the scanner must be determined. The position can be determined by the scanner using refence features on the surface being scanned (typically adhesive reflective tabs) or by using an external tracking method. External tracking often takes the form of a laser tracker (to provide the sensor position) with integrated camera (to determine the orientation of the scanner) or a photogrammetric solution using 3 or more cameras providing the complete Six degrees of freedom of the scanner. Both techniques tend to use infrared Light-emitting diodes attached to the scanner which are seen by the camera(s) through filters providing resilience to ambient lighting.
Data is collected by a computer and recorded as data points within Three-dimensional space, with processing this can be converted into a triangulated mesh and then a Computer-aided design model, often as Nonuniform rational B-spline surfaces. Hand-held laser scanners can combine this data with passive, visible-light sensors - which capture surface textures and colors - to build (or "reverse engineer") a full 3D model.
[edit] Structured light
Structured light 3D scanners project a pattern of light on the subject and look at the deformation of the pattern on the subject. The pattern may be one dimensional or two dimensional. An example of a one dimensional pattern is a line. The line is projected onto the subject using either an LCD projector or a sweeping laser. A camera, offset slightly from the pattern projector, looks at the shape of the line and uses a technique similar to triangulation to calculate the distance of every point on the line. In the case of a single-line pattern, the line is swept across the field of view to gather distance information one strip at a time.
An example of a two dimensional pattern is a grid or a line stripe pattern. A camera is used to look at the deformation of the pattern and a fairly complex algorithm is used to calculate the distance at each point in the pattern. One reason for the complexity is ambiguity. Consider an array of parallel vertical laser stripes sweeping horizontally across a target. In the simplest case, one could analyze an image and assume that the left-to-right sequence of stripes reflects the sequence of the lasers in the array, so that the leftmost image stripe is the first laser, the next one is the second laser, and so on. In non-trivial targets having holes, occlusions, and rapid depth changes, however, this sequencing breaks down as stripes are often hidden and may even appear to change order, resulting in laser stripe ambiguity. This particular problem was recently solved by a breakthrough technology called Multistripe Laser Triangulation (MLT). Structured light scanning is still a very active area of research with many research papers published each year.
The advantage of structured light 3D scanners is speed. Instead of scanning one point at a time, structured light scanners scan multiple points or the entire field of view at once. This reduces or eliminates the problem of distortion from motion. Some existing systems are capable of scanning moving objects in real-time.
Recently, Song Zhang and Peisen Huang from Stony Brook University developed a real-time scanner a using digital fringe projection and phase-shifting technique (a various structured light method). The system is able to capture, reconstruct and render the high-density details of the dynamically deformable objects (such as facial expressions) at 40 frames per second.[4]
[edit] Modulated light
Modulated light 3D scanners shine a continually changing light at the subject. Usually the light source simply cycles its amplitude in a sinusoidal pattern. A camera detects the reflected light and the amount the pattern is shifted by determines the distance the light traveled. Modulated light also allows the scanner to ignore light from sources other than a laser, so there is no interference.
[edit] Non-contact passive
Passive scanners do not emit any kind of radiation themselves, but instead rely on detecting reflected ambient radiation. Most scanners of this type detect visible light because it is a readily available ambient radiation. Other types of radiation, such as infrared could also be used. Passive methods can be very cheap, because in most cases they do not need particular hardware.
[edit] Stereoscopic
Stereoscopic systems usually employ two video cameras, slightly apart, looking at the same scene. By analyzing the slight differences between the images seen by each camera, it is possible to determine the distance at each point in the images. This method is based on human stereoscopic vision.[1]
[edit] Photometric
Photometric systems usually use a single camera, but take multiple images under varying lighting conditions. These techniques attempt to invert the image formation model in order to recover the surface orientation at each pixel.
[edit] Silhouette
These types of 3D scanners use outlines created from a sequence of photographs around a three-dimensional object against a well contrasted background. These silhouettes are extruded and intersected to form the visual hull approximation of the object. With these kinds of techniques some kind of concavities of an object (like the interior of a bowl) are not detected.
[edit] User assisted (image-based modeling)
There are other methods that, based on the user assisted detection and identification of some features and shapes on a set of different pictures of an object are able to build an approximation of the object itself. This kind of techniques are useful to build fast approximation of simple shaped objects like buildings. Various commercial packages are available like iModeller, D-Sculptor or RealViz-ImageModeler.
This sort of 3D scanning is based on the principles of photogrammetry. It is also somewhat similar in methodology to panoramic photography, except that the photos are taken of one object on a three-dimensional space in order to replicate it instead of taking a series of photos from one point in a three-dimensional space in order to replicate the surrounding environment.
[edit] Reconstruction, or Modeling
The point clouds produced by 3D scanners are usually not used directly, although for simple visualization and measurement in the architecture and construction world, points may suffice.
Most applications instead use polygonal 3D models, NURBS surface models, or editable feature-based CAD models (aka Solid models). The process of converting a point cloud into a usable 3D model in any of the forms described above is called 'reconstruction or "modeling"'.
POLYGON MESH MODELS: In a polygonal representation of a shape, a curved surface is modeled as many small faceted flat surfaces (think of a sphere modeled as a disco ball). Polygon models -- also called Mesh models, are useful for visualization, for some CAM (i.e., machining), but are generally "heavy" ( i.e., very large data sets), and are relatively un-editable in this form. Reconstruction to polygonal model involves finding and connecting adjacent points with straight lines in order to create a continuous surface. Many applications, both free and non free, are available for this purpose (eg. MeshLab, kubit PointCloud for AutoCAD, photomodeler, imagemodel, PolyWorks, Rapidform, Geomagic, Imageware, Rhino, etc.).
SURFACE MODELS: The next level of sophistication in modeling involves using a quilt of curved surface patches to model our shape. These might be NURBS, TSplines or other curved representations of curved topology. Using NURBS, our sphere is a true mathematical sphere. Some applications offer patch layout by hand but the best in class offer both automated patch layout and manual layout. These patches have the advantage of being lighter and more manipulable when exported to CAD. Surface models are somewhat editable, but only in a sculptural sense of pushing and pulling to deform the surface. This representation lends itself well to modeling organic and artistic shapes. Providers of surface modelers include Rapidform, Geomagic, Rhino, Maya, T Splines etc.
SOLID CAD MODELS: From an engineering/manufacturing perspective, the ultimate representation of a digitized shape is the editable, parametric CAD model. After all, CAD is the common "language" of industry to describe, edit and maintain the shape of the enterprise's assets. In CAD, our sphere is described by parametric features which are easily edited by changing a value(e.g., centerpoint and radius).
These CAD models describe not simply the envelope or shape of the object, but CAD models also embody the "design intent" (i.e., critical features and their relationship to other features). An example of design intent not evident in the shape alone might be a brake drum's lug bolts, which must be concentric with the hole in the center of the drum. This knowledge would drive the sequence and method of creating the CAD model; a designer with an awareness of this relationship would not design the lug bolts referenced to the outside diameter, but instead, to the center. A modeler creating a CAD model will want to include both Shape and design intent in the complete CAD model.
Vendors offer different approaches to getting to the parametric CAD model. Some export the NURBS surfaces and leave it to the CAD designer to complete the model in CAD(e.g., Geomagic, Imageware, Rhino). Others use the scan data to create an editable and verifiable feature based model that is imported into CAD with full feature tree intact, yielding a complete, native CAD model, capturing both shape and design intent (e.g. Rapidform). Still other CAD applications are robust enough to manipulate limited points or polygon models within the CAD environment(e.g., Catia).
[edit] Applications
[edit] Material processing and production
Laser scanning describes a method where a surface is sampled or scanned using laser technology. Several areas of application exist that mainly differ in the power of the lasers that are used, and in the results of the scanning process. Lasers with low power are used when the scanned surface doesn't have to be influenced, e.g. when it has to be digitized. Confocal or 3D laser scanning are methods to get information about the scanned surface.
Depending on the power of the laser, its influence on a working piece differs: lower power values are used for laser engraving, where material is partially removed by the laser. With higher powers the material becomes fluid and laser welding can be realized, or if the power is high enough to remove the material completely, then laser cutting can be performed.
Also for rapid prototyping a laser scanning procedure is used when for example a prototype is generated by laser sintering.
The principle that is used for all these applications is the same: software that runs on a PC or an embedded system and that controls the complete process is connected with a scanner card. That card converts the received vector data to movement information which is sent to the scanhead. This scanhead consists of two mirrors that are able to deflect the laser beam in one level (X- and Y-coordinate). The third dimension is - if necessary - realized by a specific optic that is able to move the laser's focal point in the depth-direction (Z-axis).
The third dimension is needed for some special applications like the rapid prototyping where an object is built up layer by layer or for in-glass-marking where the laser has to influence the material at specific positions within it. For these cases it is important that the laser has as small a focal point as possible.
For enhanced laser scanning applications and/or high material throughput during production, scanning systems with more than one scanhead are used. Here the software has to control what is done exactly within such a multihead application: it is possible that all available heads have to mark the same to finish processing faster or that the heads mark one single job in parallel where every scanhead performs a part of the job in case of large working areas.
Structured light projection systems are also used for solar cell flatness metrology enabling stress calculation with throughput in excess of 2000 wafers per hour. [5]
[edit] Construction industry and civil engineering
- As-built drawings of Bridges, Industrial Plants, and Monuments
- Documentation of historical sites
- Site modeling and lay outing
- Quality control
- Quantity Surveys
- Freeway Redesign
- Establishing a bench mark of pre-existing shape/state in order to detect structural changes resulting from exposure to extreme loadings such as earthquake, vessel/truck impact or fire.
- Create GIS (Geographic information system) maps and Geomatics.
[edit] Entertainment
3D scanners are used by the entertainment industry to create digital 3D models for both movies and video games. In cases where a real-world equivalent of a model exists, it is much faster to scan the real-world object than to manually create a model using 3D modeling software. Frequently, artists sculpt physical models of what they want and scan them into digital form rather than directly creating digital models on a computer.
[edit] Reverse engineering
Reverse engineering of a mechanical component requires a precise digital model of the objects to be reproduced. Rather than a set of points a precise digital model can be represented by a polygon mesh, a set of flat or curved NURBS surfaces, or ideally for mechanical components, a CAD solid model. A 3D scanner can be used to digitize free-form or gradually changing shaped components as well as prismatic geometries whereas a coordinate measuring machine is usually used only to determine simple dimensions of a highly prismatic model. These data points are then processed to create a usable digital model, usually using specialized reverse engineering software (see Modeling; Solid Models, above).
[edit] Cultural Heritage

There have been many research projects undertook the scanning of historical sites and artifacts both for documentation and analysis purposes.
The combined use of 3D scanning and 3D printing technologies allows the replication of real objects without the use of traditional plaster casting techniques, that in many cases can be too invasive for being performed on precious or delicate cultural heritage artifacts. In the side figure the gargoyle model on the left was digitally acquired by using a 3D scanner and the produced 3D data was processed using MeshLab. The resulting digital 3D model, shown in the screen of the laptop, was used by a rapid prototyping machine to create a real resin replica of original object.
[edit] Michelangelo
In 1999, two different research groups started scanning Michelangelo's statues. Stanford University with a group led by Marc Levoy[6] used a custom laser triangulation scanner built by Cyberware to scan Michelangelo’s statues in Florence, notably the David, the Prigioni and the four statues in The Medici Chapel. The scans produced a data point density of one sample per 0.25mm, detailed enough to see Michelangelo’s chisel marks. These detailed scans produced a huge amount of data (up to 32 gigabytes) and processing the data from his scans took 5 months. Approximately in the same period a research group from IBM, led by H. Rushmeier and F. Bernardini scanned the Pietà of Florence acquiring both geometric and color details.
[edit] Monticello
In 2002, David Luebke, et al. scanned Thomas Jefferson’s Monticello.[7] A commercial time of flight laser scanner, the DeltaSphere 3000, was used. The scanner data was later combined with color data from digital photographs to create the Virtual Monticello, and the Jefferson’s Cabinet exhibits in the New Orleans Museum of Art in 2003. The Virtual Monticello exhibit simulated a window looking into Jefferson’s Library. The exhibit consisted of a rear projection display on a wall and a pair of stereo glasses for the viewer. The glasses, combined with polarized projectors, provided a 3D effect. Position tracking hardware on the glasses allowed the display to adapt as the viewer moves around, creating the illusion that the display is actually a hole in the wall looking into Jefferson’s Library. The Jefferson’s Cabinet exhibit was a barrier stereogram (essentially a non-active hologram that appears different from different angles) of Jefferson’s Cabinet
[edit] Cuneiform tablets
In 2003, Subodh Kumar, et al. undertook the 3D scanning of ancient cuneiform tablets.[8] Again, a laser triangulation scanner was used. The tablets were scanned on a regular grid pattern at a resolution of 0.025 mm.
[edit] “Plastico di Roma antica”
In 2005, Gabriele Guidi, et al. scanned the “Plastico di Roma antica”,[9] a model of Rome created in the last century. Neither the triangulation method, nor the time of flight method satisfied the requirements of this project because the item to be scanned was both large and contained small details. They found though, that a modulated light scanner was able to provide both the ability to scan an object the size of the model and the accuracy that was needed. The modulated light scanner was supplemented by a triangulation scanner which was used to scan some parts of the model.
[edit] Dental CAD/CAM
Many Chairside dental CAD/CAM systems and Dental Laboratory CAD/CAM systems use 3D Scanner technologies to capture the 3D surface of a dental preparation (either in vivo or in vitro), in order to produce a restoration digitally using CAD software and ultimately produce the final restoration using a CAM technology (such as a CNC milling machine, or 3D printer). The chairside systems are designed to facilitate the 3D scanning of a preparation in vivo and produce the restoration (such as a Crown, Onlay, Inlay or Veneer).
[edit] Orthotics CAD/CAM
Many orthotists also use 3D scanners in order to capture the 3D shape of a patient. It gradually supplants tedious plaster cast. CAD/CAM software are then used to design and manufacture the orthosis or prosthesis.
[edit] Quality assurance
The digitalization of real-world objects is of vital importance in various application domains. This method is especially applied in industrial quality assurance to measure the geometric dimension accuracy. Industrial processes such as assembly are complex, highly automated and typically based on CAD (Computer Aided Design) data. The problem is that the same degree of automation is also required for quality assurance. It is, for example, a very complex task to assemble a modern car, since it consists of many parts that must fit together at the very end of the production line. The optimal performance of this process is guaranteed by quality assurance systems. Especially the geometry of the metal parts must be checked in order to assure that they have the correct dimensions, fit together and finally work reliably.
Within highly automated processes, the resulting geometric measures are transferred to machines that manufacture the desired objects. Due to mechanical uncertainties and abrasions, the result may differ from its digital nominal. In order to automatically capture and evaluate these deviations, the manufactured part must be digitized as well. For this purpose, 3D scanners are applied to generate point samples from the object’s surface which are finally compared against the nominal data [10]. Particularly tactile and optical scanners are used to obtain the 3D measures. The small size and simple construction of the wearless working optical scanners enable a flexible application, and thus replace the approved tactile systems more and more.
[edit] See also
[edit] References
This article includes a list of references or external links, but its sources remain unclear because it lacks inline citations. Please improve this article by introducing more precise citations where appropriate. |
- Brian Curless, "From Range Scans to 3D Models", ACM SIGGRAPH Computer Graphics, Vol. 33, Issue 4, Nov 2000, pp.38-41.
- Katsushi Lkeuchi, "Modeling from Reality," Third International Conference on 3-D Digital Imaging and Modeling, 2001, pp.117-124.
- ^ Fausto Bernardini, Holly E. Rushmeier: The 3D Model Acquisition Pipeline. Comput. Graph. Forum 21(2): 149-172 (2002), (pdf).
- ^ Roy Mayer, Scientific Canadian: Invention and Innovation From Canada's National Research Council, Vancouver: Raincoast Books, 1999.
- ^ François Blais, Michel Picard, Guy Godin, "Accurate 3D acquisition of freely moving objects," Proceedings. 2nd International Symposium on 3D Data Processing, Visualization and Transmission, 2004, pp.422-429.
- ^ Song Zhang, Peisen Huang, "High-resolution, real-time 3-D shape measurement," Optical Engineering, 2006, pp.123601. (pdf)
- ^ W. J. Walecki, F. Szondy and M. M. Hilali, "Fast in-line surface topography metrology enabling stress calculation for solar cell manufacturing for throughput in excess of 2000 wafers per hour" 2008 Meas. Sci. Technol. 19 025302 (6pp) doi:10.1088/0957-0233/19/2/025302
- ^ Marc Levoy, Jeremy Ginsberg, Jonathan Shade, Duane Fulk, Kari Pulli, Brian Curless, Szymon Rusinkiewicz, David Koller, Lucas Pereira, Matt Ginzton, Sean Anderson, James Davis, "The Digital Michelangelo Project: 3D Scanning of Large Statues," Proceedings of the 27th annual conference on Computer graphics and interactive techniques, 2000, pp.131-144. (pdf)
- ^ David Luebke, Christopher Lutz, Rui Wang, and Cliff Woolley, “Scanning Monticello,” 2002, http://www.cs.virginia.edu/Monticello.
- ^ Subodh Kumar, Dean Snyder, Donald Duncan, Jonathan Cohen, Jerry Cooper, "Digital Preservation of Ancient Cuneiform Tablets Using 3D-Scanning," Fourth International Conference on 3-D Digital Imaging and Modeling, 2003, pp.326-333.
- ^ Gabriele Guidi, Laura Micoli, Michele Russo, Bernard Frischer, Monica De Simone, Alessandro Spinetti, Luca Carosso, "3D digitization of a large model of imperial Rome," Fifth International Conference on 3-D Digital Imaging and Modeling, 2005, pp.565-572.
- ^ Christian Teutsch, "Model-based Analysis and Evaluation of Point Sets from Optical 3D Laser Scanners", PhD Dissertation, 2007.
[edit] External links
- 3D Photography Course Notes
- MeshLab - Open Source program for aligning, merging, cleaning up and simplifying scanned meshes
- Scanalyze - Open Source program for aligning and merge range data
- Manual 3D scanner 3D scan technology description
- Free 3D Scanner Routines -- Software from Laurence Hassebrook at University of Kentucky for use with PowerShot or Logitech WebCam.